公差解析:机械设计中的允许误差范围与制造精度控制
adminc2025-05-09篮球赛事20 浏览
在机械设计与制造中,公差控制是确保零件功能性与互换性的核心要素。它不仅影响产品的装配效果和使用寿命,还直接决定了生产成本和效率。本文将从基础概念、控制策略到实际应用,系统解析机械设计中允许误差范围的管理方法,并提供行业内的实用建议。
一、公差的基本概念与重要性
公差是零件实际参数值允许的变动量,其本质是通过限定误差范围来平衡加工精度与成本。例如,一个孔径的基本尺寸为30mm,若最大极限尺寸为30.010mm,最小极限尺寸为29.990mm,则公差为0.020mm,上下偏差分别为+0.010和-0.010mm。
核心术语解析:
基本尺寸:设计时确定的理想尺寸。
极限尺寸:允许的最大和最小尺寸边界。
公差带:由上下偏差限定的区域,包含公差大小和位置两个要素。
标准公差等级:国际标准(ISO)将公差分为20个等级(IT01至IT18),等级越高,公差值越小,精度要求越严格。
为何需要公差控制?
零件加工时,机床精度、刀具磨损等因素必然导致误差。合理的公差设计能避免因过度追求精度而增加成本,同时确保零件在装配中的互换性和功能稳定性。
二、公差等级与标准体系的选择
1. 公差等级的应用场景
IT01-IT4级:用于高精密量具、航空航天等特殊领域,如标准量块、精密轴承配合。
IT5-IT7级:常见于汽车、精密机械的关键配合部件,如发动机活塞与缸体的配合。
IT8-IT11级:适用于一般机械零件,如外壳、非关键连接件。
2. 国际公差标准体系
ISO 2768:针对未注公差的线性尺寸、角度和倒角,分精密级(F)和中等级(M)。例如,30-120mm的线性尺寸中等级公差为±0.3mm。
ISO 286:适用于轴孔配合,分为IT6、IT7、IT8等级。例如,直径18-30mm的轴,IT7级公差为0.021mm。
选择建议:
优先采用基孔制(以孔为基准)简化加工。
根据零件功能需求选择等级,非关键部位可放宽至IT11级以降低成本。
三、制造精度的控制策略
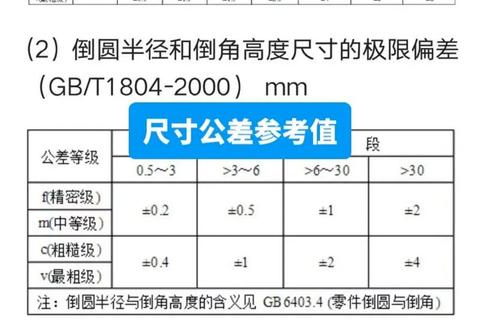
1. 设计阶段的公差分配
包容原则:确保孔轴配合时,实际要素在最大实体边界内,适用于精密配合。
独立原则:尺寸与形位公差分别控制,用于非配合结构(如倒角)。
2. 工艺优化方法
虚拟验证:通过尺寸链分析和3D仿真预测公差叠加效应,减少试错成本。
夹具与定位优化:减少加工中的定位误差,例如白车身工艺基准RPS点的标准化。
3. 测量与反馈机制
三坐标测量(CMM):检测复杂形位公差(如平行度、圆度)。
统计过程控制(SPC):实时监控生产数据,调整工艺参数。
四、实用建议:如何平衡精度与成本
1. 标注规范:
优先采用“公差带代号+偏差值”标注(如Φ60H7),兼顾可读性与加工指导。
非关键尺寸使用通用公差标准(如ISO 2768-M),减少标注工作量。
2. 材料与工艺匹配:
硬质材料(如淬火钢)可承受更严苛的公差,而软材料(如铝合金)需适当放宽。
3. 成本控制技巧:
对非功能面采用“未注公差”,默认按IT12级加工。
批量生产中,分组装配法可降低单个零件精度要求。
五、案例解析与行业应用
案例1:汽车发动机曲轴加工
曲轴轴颈需与轴承高精度配合(IT6级)。通过优化工艺路线(粗车→热处理→精磨)和采用主动测量补偿系统,将公差控制在0.01mm内,同时减少废品率。
案例2:电子连接器引脚间距
引脚间距公差过大会导致接触不良。采用最大实体要求(MMR),允许形位公差补偿尺寸误差,确保0.05mm的定位精度。
六、未来趋势:数字化与智能化
公差分析软件:如三维公差堆栈分析工具,可自动模拟装配偏差。
AI驱动的工艺优化:利用机器学习预测加工误差,动态调整公差参数。
通过科学的公差设计与制造控制,企业能在保证产品质量的前提下显著降低成本。对于工程师而言,掌握公差等级选择、标准应用及工艺优化方法,是提升核心竞争力的关键。未来,随着数字化工具的普及,公差管理将更加高效精准,推动制造业向更高水平迈进。